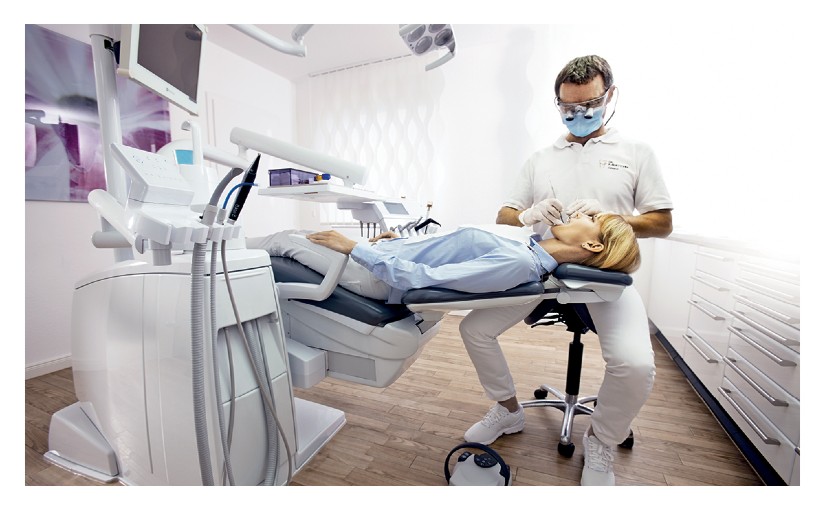
A Brief Discussion Document on Equipment and Local Infection Control Requirements, from an Equipment Technical Perspective
When we move to dental equipment, most clinicians choose from mainstream manufacturers. These companies have become mainstream by providing a consistent quality offering to the market, appropriate and fit for purpose.
From their factories, they’ve studied materials, design, infection control and of course costs to strike a balance of a product fit for purpose and of universal appeal to assure their commercial success. Their care instructions by necessity are designed to provide a universal guide, striving for a common and global denominator on how to care for the equipment and how to achieve an acceptable level of infection control without compromising longevity or function.
Some documents will suggest what to do but not name a product, some will name a product and others will suggest what not to use. You’d be forgiven for expressing frustration, why don’t we have more products on the approved list. There is a simple explanation in part, found in your catalogue pile at the office. You’ve probably choices of 10’s if not 100’s of infection control consumables, catering for our 16,500 or so dentists. Taking a world view with 700,000 dentists, extrapolate these to the smaller chemical companies to a global count; it’s almost enough to toss it all in and buy a gin distillery to manufacture hand sanitiser.
The logic becomes apparent; global equipment companies select global material companies. Companies such as Durr, Kerr and Alpro to name a couple are able to reach their same worldwide client base and are the ideal partners to select and spend the significant time and money to test, identify and approve products that are of a known quality to protect you their clients.
Our shared problem hits when Australian Guidelines and the manufacturer recommendations don’t line up, or the guidelines place additional stress on your equipment.
Our first recommendation is to follow the Australian guidelines. The defence, “officer I didn’t know the speed limit was 50km/h”, is not a defence. As a self-regulating practice, your documented adherence to the expert prevailing advise, is your correct response.
Our next recommendation is you should follow the manufactures guidelines where they align with our local expert advice. When a choice exists to choose a product they recommend, you should select that product as you’ll know it’s been tested to perform the task without detriment to the equipment.
I know it’s un-Australian to suggest this; read the instructions. Chemistry, processes in cleaning and disinfection is well researched. Follow the instructions to the letter.
When it comes to diluting chemistry, if the instruction says 35ml, that’s not a splash, it’s not about 50ml. Some of the most epic material failures we’ve seen over the decades are from the splash and dash approach to inexpensive cleaners and disinfectants rendering havoc on expensive equipment. Dilution matters.
Based on the above, 35ml example if it were a Gin and Tonic, you’ve just added 43% more Gin, possibly fun, definitely more costly and likely causing damage (that’ll creep up on you).
When it comes to selecting chemistry for cleaning, consider the whole product. By that we mean, please don’t stop reading at neutral pH detergent, sounds perfect right? Perhaps not, what if the document revealed it had EDTA, or formaldehyde additives in the mix? Understanding what you are purchasing can touch on multiple areas, including applicability, maintenance impact and even OH&S considerations too.
Our recommendation when selecting cleaning and disinfection products for equipment, where the manufacturer has not named a specific product. In this case read the intent of the instruction, then consider the intent of the product. Do these two aspects align with what you need, if not grab your Henry Schein rep and look for alternatives?
For example; Planmeca says, ‘clean with neutral pH detergent’ (they’ve not specified product). Our Aussie protocol says remove bioburden with neutral or slightly alkaline detergent and rinse. From this we surmise; it looks like we have an alignment with both manufacturer and Aussie standards.
We then move to intent of the product selected. We’re cleaning a medical device. Is the specific product tested and recommended for medical device surfaces?
This is important, your dental equipment is medical equipment, don’t use products designed for floors or bedpans and trolleys. Medical equipment is more delicate, and products for medical equipment is quite different to hospital surface cleaners or disinfectants. Expensive damage has been done by not recognising these distinctions matter.
This advice also applies to the internal surfaces, waterline products and suction cleaners. Although hidden from view, just using any old thing, or ignoring the process has led to plenty of unexpected and unwanted service visits as the practice screams to a stop on a seized motor.
Remember to take into account the enthusiasm of the salesperson, it’s key to the job description. They’ve received glowing recommendations from the maker that it’s great, it’s a great price etc. In good faith they may be making a recommendation, that with hindsight perhaps was wanting.
When we see damage to equipment for not using the appropriate products correctly, it’s not like flipping a switch, this damage generally is cumulative and changes things slowly over weeks or months. If it’s degrading the composition of the materials, often things go from looking OK to just falling apart.
With this in mind to add a further recommendation, experience counts. If you are using a product not specifically named by the manufacturer and it passes the initial investigation. Tread conservatively; that old adage of test in an inconspicuous spot is good advice. Use it for a while and look for changes, compare highly cleaned areas to areas less touched – is the surface that gets wiped every patient still looking the same as that hidden away spot under the chair that barely gets touched? Do this over weeks if not months.
A quick note on your wipes, please use cleaning wipes, designed for the purpose medical wipes have a design to lift and capture the bioburden and not abrade surfaces. Substituting paper towels can be tempting but abrasive. You’d never clean your spectacles with a paper towel. Imagine now the cumulative damage of cleaning your equipment eight times a day, five days a week for five years of the unit’s life.
Lastly, you’ve done everything right and the equipment under the load of disassembly, cleaning, disinfection, sterilisation, lubricated things that need to be lubricated and reassembled. You’ve checked and documented your infection control protocols, checked to see that policy creep has not happened with staff changes or changed products due to the deal of the month.
And…
The equipment is still getting old.
Our last recommendation in this essay is to rinse. Plain old water and a non-abrasive wipe. All the above protocols and procedures often leave a small film of chemistry that simply sits there, builds up in some cases and keeps the reaction going on your surfaces.
Using water and cloth to remove all chemical residues, leaves your equipment squeaky clean. If there are no residues or stickiness left, there is no bioburden remaining and no ongoing reactions to prematurely age your equipment. A win win in an equipment/infection control environment.
Concluding, under intense load, infection control longevity can be challenged. We expect following the manufacturers recommendations closely, the outcome will maximise your equipment’s life and appearance in a challenging environment. We have a terrific depth of expertise at Henry Schein and stand ready to help, if you’d like to discuss any aspect of this essay or would like specific product information please reach out to the team.